What is Muda? The 7 Waste in Lean Manufacturing
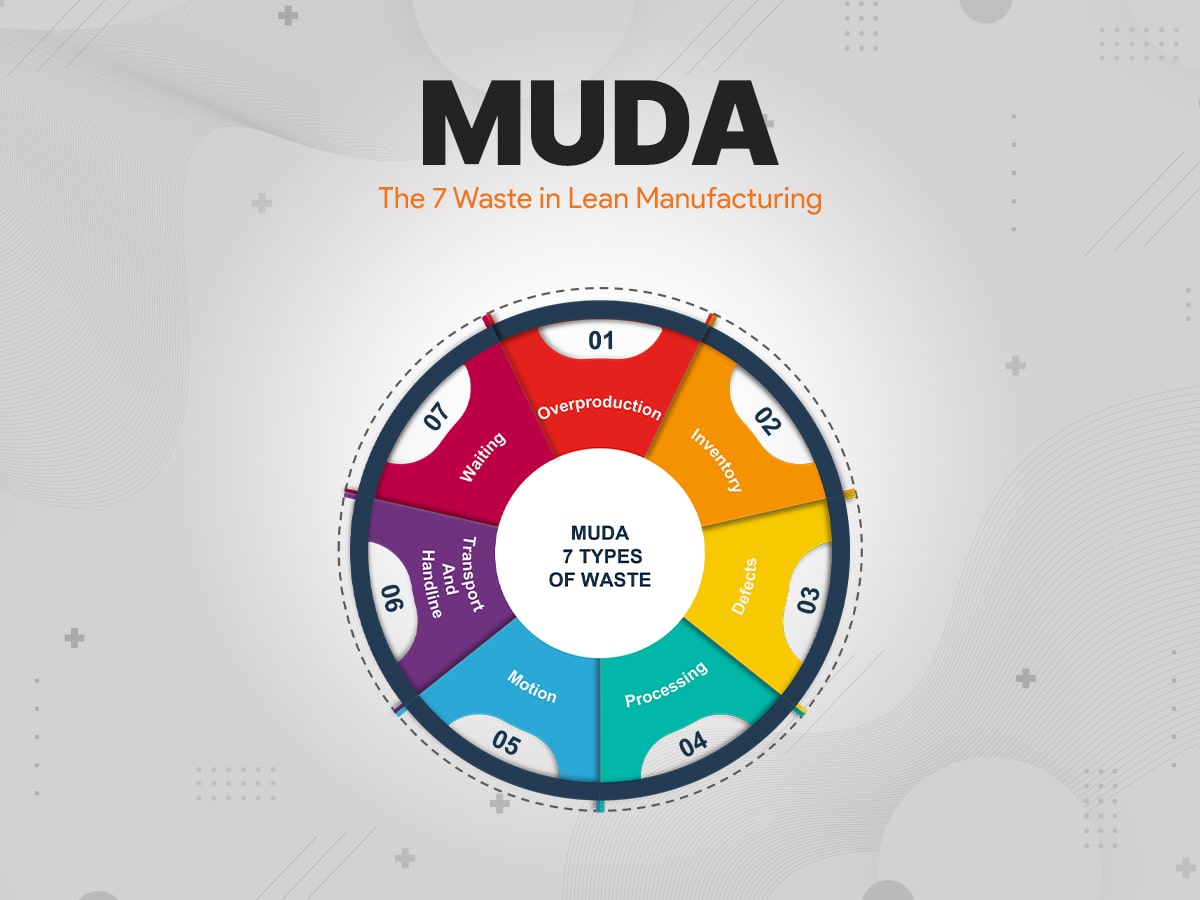
One of the major parts of driving your industry forward is being able to identify and tackle waste. To improve the profitability of the business, waste elimination is one of the effective ways. The concept of “Muda” 7 waste originated in Japan, in Japanese language Muda means Waste. The 7 waste is an instrument to further group “Muda” and was initially developed by Toyota Chief Taiichi Ohno as the core Toyota Production System, also famous as lean manufacturing. Lean manufacturing is an approach that focuses on reducing waste within manufacturing systems while simultaneously maximizing productivity.
Today, Corporate PowerPoint Presentation also focused on the improvement of profitability through minimizing industry waste. Lean manufacturing is grounded on a number of definite principles, such as Kaizen, or continuous improvement. To minimize waste, it is important to understand exactly what waste is and where it exists. Though products considerably differ between factories, the usual wastes found in manufacturing environments are quite similar. For each waste, there is a plan to reduce or remove its effect on a company, thereby improving overall performance and quality.
How to categorize” Waste” and “Non-Waste
We can simply describe that waste is “something that adds no value”. While non-waste is the just opposite of this definition. Value is created by the producer, but it’s defined by the customer. That is, businesses need to understand the value the customer places on their product/services, which, in turn, can help them determine how much money the customer is willing to pay. Following are the 7 wastes, classified by Taiichi Ohno.
1. Overproduction
Manufacture of products in advance or in excess of demand wastes money, space and time. It is the production of goods before it is actually required. This advanced production waste results from producing more than required. This would be highly costly to the industry because it hinders the easy flow of materials and truly degrades quality and productivity. Toyota produced its goods “just in Time” because every product is made just as it is needed. Overproduction results in high storage cost, excessive lead times, and makes hard to identify defects. To solve this problem you should turn off the production pipeline; this required a lot of courage because the problems that excessive production is hiding will be revealed. The core idea behind this concept is to produce and schedule only what can be immediately shipped/sold and improve machine changeover or set-up capability.
2. Waiting
It is the act of doing nothing or working slowly whilst waiting for a preceding step in the process. The waste of waiting occurs whenever goods are not moving or under processing. Whenever the flow of operation would be on sluggish, the production process will lose its continuity. Studies show, more than 99% of the product will be spent waiting to be processed. You pay for the time spent by all of your staffs, time that they do not spend adding value while they are waiting. If you try to make up with this by overtime, it will not benefit you, but well for your employees. There are several types of wastes of Waiting. For example, waiting for information from the designing department or waiting to be told which product is required next.
3. Transporting
Moving in-process items from one unit to another is an example of transportation waste; it adds no value to the product. Unnecessary movement and handling cause and are a chance for quality to deteriorate. Transportation can be difficult to reduce due to the supposed costs of moving equipment and processes closer together. This waste is an impediment to achievement a lean manufacturing operation. If the assembly line works properly you can eliminate transportation “Muda”.
4. Inappropriate Processing
Instead of a simpler type of machinery, many industries use high precision equipment’s. This often results in poor plant designing because previous or subsequent operations are located far apart. The bigger machines that can do an operation quicker than any other, but every process flow has to be directed through it creating planning complications, intervals and so on. Low-cost automation is suggested by Toyota can be admired by others. Financing in simple, more flexible equipment where possible; building manufacturing cells; and integrating step will precisely reduce the Muda of inappropriate processing.
5. Excessive Inventory
Inventory is the WIP (work in progress), the raw materials, and the finished goods that kept in warehouses. Every single piece of inventory you hold has a physical cost associated with it, that cost is carried directly by yourself either from your cash or from borrowing for which you will be charged interest. WIP and the stocks of finished products is a direct result of overproduction. Unnecessary inventory increases lead times, consumes productive floor space, delays the detection of problems, and obstruct communication.
6. Unnecessary Motion
If the workers take more time to reach one place to another, it is the 6the Muda of 7 wastes. Resources are wasted when workers have to bend, reach or walk distances to do their jobs. Workstation ergonomics studies should be accompanied to design a more efficient environment. Moving is not necessarily working. Poor workstation layout results in excessive motion. There are also safety and health issues, which in today’s litigious society are becoming more of a problem for the organization. Works with excessive motion should be analyzed and redesigned for improvement with the involvement of the plant manager.
7. Defects
Defects are when the products/services deviate from what the customer requires. Defects in quality, resulting in rework or scrap are a tremendous cost to organizations. Checking and quarantining inventory takes time, and it costs money. In many industries, the entire cost of defects is often a major percentage of total manufacturing cost.
The 7 waste management presentation can be illustrated using a suitable PowerPoint, which showcasing the topic with metaphors. For this purpose, slide bazaar has been introduced Muda 7 wastes PowerPoint template and related templates such as continual improvement process template for PowerPoint and keynote and lean manufacturing PowerPoint template and keynote slide.