Definition, components and process of quality management
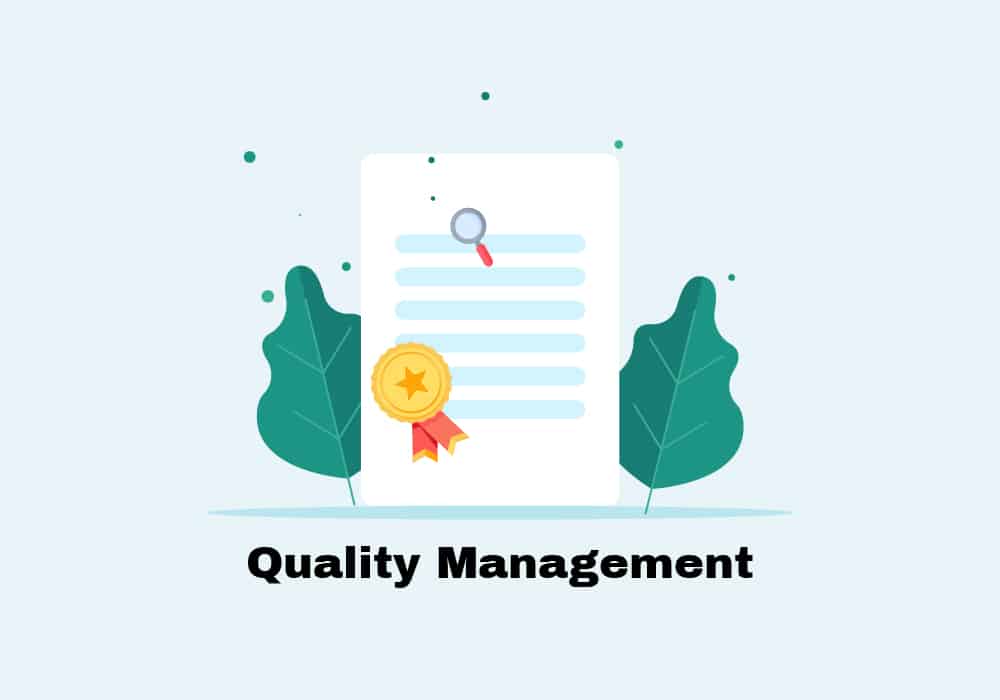
Hey, that product has no quality; I have bought it a few weeks ago, now it’s not working properly. This is the common statement of a person featuring the product what he bought when it not showing expected results. Do such comment beneficial for the company which produces the device? Why public does opine such a way? Here, the concept of quality management arises.
Definition of quality management
Quality management is the act of supervision of all activities and tasks that must be accomplished to maintain a preferred level of quality. This comprises the purpose of a quality policy, forming and applying quality planning and assurance, and quality control and quality improvement. It is also denoted to as total quality management (TQM).
Four key components of Quality Management
- Quality Planning – The process of identifying the quality standards relevant to the project and deciding how to attain them.
- Quality Improvement – The determined change of a process to improve the confidence, reliability and consistency of the outcome.
- Quality Control – The enduring effort to uphold a process’s integrity and reliability in realizing an outcome.
- Quality Assurance – The organized or the planned actions necessary to offer sufficient reliability that a particular service/product will meet the definite requirements.
History of Total Quality Management (TQM)
While Total quality management seems like an intuitive process, it originates as a revolutionary concept. The 1920s saw the augmentation in reliance on statistics and statistical theory in business, and the first-ever known control chart was made in 1924. People began to build on ideas of statistics and ended up jointly creating the method of statistical process control (SPC). However, it wasn’t effectively executed in a business setting until the 1950s.
In the mid 20th century the concept of quality management has originated in Japan. At that time, Japan was facing serious industrial problems, their products were considered to be low quality and the citizens were thought to be illiterate. Key businesses in Japan saw these deficiencies and viewed to make a change. Trusting on pioneers in statistical thinking, companies such as Toyota incorporated the idea of quality management and quality control into their manufacturing processes. By the end of the 1960s, Japan completely implemented quality management measures and became known as one of the most efficient export countries, with some of the most appreciated products. Effective quality management resulted in better products that could be produced at a low-cost price.
The process of quality management
The process of TQM comprises a set of procedures that are developed by a team to ensure that the products/services that they produce are of the right standards or adequate for the purpose.
- The process begins when the organization sets quality targets to be achieved and which are agreed upon with the customer.
- The organization describes how the targets will be measured. It takes actions that are essential to measuring quality. They then identify any quality matters that arise and initiate improvements.
- The last step includes reporting the overall level of the quality attained.
The quality improvement methods mainly include three components: product improvement, process improvement, and people-based improvement. There are several methods of quality management and techniques that can be utilized. They include Kaban, Kaizen, Six Sigma, Quality Circle, Zero Defect Programs Taguchi Methods, the Toyota Production System, Kansei Engineering, BPR, TRIZ, OQRM, ISO, and Top-Down & Bottom-Up methods among others.
An excellent example of quality management is the implementation of the Kanban system by Toyota Corporation. Kanban is an inventory control system that was developed by Taiichi Ohno to generate visibility for both the suppliers and customers to help limit the increase of extra inventory on the production streak at any given point in time. Toyota used the concept to implement its Just-in-time (JIT) system, which helps align raw material orders from dealers directly with the production timetables. Toyota’s assembly line rose in effectiveness and the company established enough inventories at hand to meet customer orders as they were being created.
help template:muda 7 waste powerpoint
Principles of Quality Management
Quality management has been adopted several standards at international level. All these standards are considered to be the principles of quality management. These principles are used by top management to guide an organization’s processes towards better performance. They include:
- Customer-related
Every organization gives more importance to its customers. The primary focus of any business should be to meet and exceed the customers’ expectations and needs. When an organization can understand the customers’ current and future needs and provide to them, it results in customer loyalty, which in turn increases income. The business is also able to get new customer opportunities and please them. When business processes are more competent, quality is higher and more customers can be pleased.
- Leadership
Good leadership is the foundation of company success. Effective leadership establishes harmony and purpose among the workforce and shareholders. Creating a prospering company culture offers an internal environment that lets employees to fully utilize their potential talents and get actively involved in achieving its purposes. The leaders should involve the employees in setting clear organizational aims and intentions. It inspires employees, who can significantly improve their output and loyalty.
- Engagement of People
Staff participation is another vital principle. The management engages staff in creating and carrying value whether they are full-time, part-time, outsourced, or in-house. An organization should inspire the employees to continually improve their skills and maintain stability. This principle also includes empowering the employees, involving them in decision making and identifying their accomplishments. When people are valued, they work to their best potential because it lifts their confidence and motivation. When workers are entirely involved, it makes them feel empowered and responsible for their actions.
- Process Approach
The performance of a company is crucial according to the process approach principle. The approach stresses on attaining efficiency and effectiveness in the organizational processes. The approach involves an understanding that good processes result in improved stability, quicker doings, reduced costs, waste elimination, and continuous improvement. An organization is improved when leaders can regulate and control the inputs and the outputs of an organization, as well as the procedures used to produce the outputs.
- Continuous Improvement
Every organization should come up with an aim to be actively involved in continuous improvement. Businesses that progress continually experience better performance, organizational flexibility and increased ability to hold new opportunities. Businesses should be able to make new processes continually and adjust to new market situations.
- Evidence-based Decision Making
Businesses should adopt a realistic approach to decision-making. Businesses that make decisions based on verified and studied data have an improved understanding of the marketplace. They are capable to do tasks that produce anticipated results and even justify their past judgments. Actual decision making is vital to help know the cause-and-effect connections of different things and even describe potential unintended results and its impacts.
- Relationship Management
Relationship management is about creating reciprocally beneficial relations with suppliers and retailers. Different interested parties can impact the company’s performance. The organization should be able to control the supply chain process well and encourage the relationship between the organization and its suppliers to improve their impact on the company’s performance. When an organization manages its relationship with interested parties well, it is more likely to achieve a continued business relationship.
Advantages of quality management
- It aids an organization to attain greater consistency in tasks and activities that are involved in the production of products and services.
- It enhances efficiency in processes, reduces wastage, and improves the use of time and other resources.
- It helps improve customer satisfaction.
- It allows businesses to market their business effectively and exploit new markets.
- It makes it easier for businesses to incorporate new employees and thus helps businesses manage growth more effortlessly.
- It supports a business to continuously improve their products, processes, and systems.
Strategic Planning and Quality Control
Having a focus and a strong perspective on quality in production and in work levels lets employees at all ranks to constantly plan for improvements. The consciousness of a desire for perfection in workplace actions and an emphasis on stability, consistency and steadiness will help to encourage productive processes for generating products and managing customer satisfaction. Strategic planning also includes quality control.
Quality control is also accountable for quickness of distribution of products, company-wide compliance with processes, removing waste within production and workers and keeping every member of the team concentrated on an emphasis on buyer satisfaction.
Quality management in businesses is essential to confirm consistency in its procedures, as well as its products and services. In business, customer satisfaction is the most important thing. As a customer’s prime concern is the quality of the product/ services they purchase, the dealer’s main aim should always be to ensure that what they create is of reliable and fine quality.